Avmount
Vibro Dampers are designed to use the isolating media, rubber
in this case, both in compression and in shear. It is bonded
to metal during vulcanisation such that the design makes the
mounting have an equal stiffness in all directions. The mounting
can be used for mobile applications also, since the base of
the mounting is provided with holes for attachment to the
chassis. It also has a friction pad bonded to the bottom of
the base for proper fixation of the machine to the floor in
case of stationary applications. Hence no bolting is necessary
under these conditions.
Avmount
Vibro Dampers are highly efficient yet economical vibration
and shock isolators. This product is EXCLUSIVELY manufactured
by us. You can use them for vibration of compressors, diesel
generators, fans and motors as well as for the protection
of mounted equipment from external vibration or shock. Being
of extremely robust design, these isolators are particularly
suitable for rugged conditions and give trouble-free and continued
service. Their life is generally equal to that of the machinery
or plant which is mounted on them.
Avmount Vibro Dampers Type AVM in addition to isolating machinery
and structures from vibration and shock, provide a means sitting
stabilisation so that the floor areas are undisturbed with
no need for bolting or grouting in. machinery is left free-standing
and thus can be re-sitted with ease. To meet certain requirements,
however, holes are provided in the base plate.
Machinery mounted on our dampers is isolated both actively
and passively. The machinery is isolated actively in the sense
that the machine which is a source of vibration is so isolated
that the incidence of transmission of vibration to the floor
upon which it rests is reduced to an extent, and passively
in the sense that the machine which would be affected adversely
by external sources of vibration is now insulated from them.
Avmount
Vibro Dampers Type AVM have a bottom friction pad bounded
to the bottom of the mounting and hence there is no necessity
of adding another friction pad.
Dimensions
of Vibro Dampers (Type AVM)
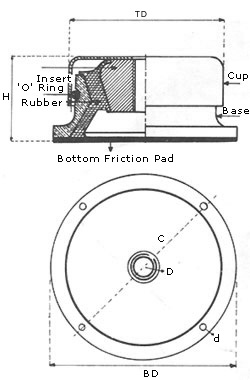
|
TD |
BD |
Free
H |
D |
PCD'C' |
Diameter'd' |
Type AVM 60/120 |
58
mm |
80 |
40.5 |
M10 |
65 |
7
mm |
Type
AVM 75/180 |
78
mm |
115 |
50.5 |
M12 |
95 |
9
mm |
Type AVM 225/375 |
100
mm |
150 |
59.5 |
M16 |
120 |
11
mm |
Type AVM 300/800 |
125
mm |
185 |
72.5 |
M20 |
150 |
13
mm |
Technical
Specifications of Vibro Dampers (Type AVM)
Type |
Shore
Hardness |
F |
d |
Fn |
%
Isolation at fd |
1000
rpm |
1500
rpm |
AVM 60/120A
60/120B
60/120C |
45
55
65 |
60
kg
90 kg
120 kg |
4.4
mm
4.1 mm
4.3 mm |
8.6
Hz
8.9 Hz
8.7 Hz |
60
60
60 |
87
85
85 |
AVM
75/180A
75/180B
75/180C |
45
55
65 |
75
kg
120 kg
180 kg |
5.8
mm
5.8 mm
5.9 mm |
7.5
Hz
7.5 Hz
7.4 Hz |
73
73
74 |
88
88
89 |
AVM 225/375A
225/375B
225/375C |
45
55
65 |
225
kg
275 kg
375 kg |
5.9
mm
6.0 mm
6.2 mm |
7.4
Hz
7.3 Hz
7.2 Hz |
74
75
76 |
89
90
91 |
AVM
300/800A
300/800B
300/800C |
45
55
65 |
300
kg
500 kg
800 kg |
5.8
mm
6.3 mm
5.3 mm |
7.5
Hz
7.1 Hz
7.8 Hz |
73
77
70 |
88
92
87 |
d
= deflection at rated load
Fn = Natural frequency at rated load and deflection
fd = Disturbing frequency
F
= Rated load/mount
Note: It is essential that all mounts deflect equally so that
the system has a single natural frequency and not different
natural frequencies at each point.

VIBRO DAMPERS
Installation
of equipments on VIBRO DAMPERS is the modern method of installing
equipment which must be protected from shock and vibrations
which are inherent in many environments.
In mobile applications the equipments remains steady and isolated
from the base vibrations during transit.
Type
AVM 120/280
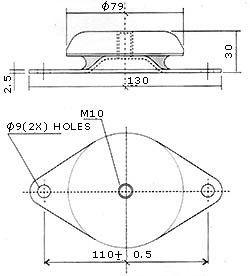
Mount
type |
Shore
hardness |
Rated
load / mount |
Deflection
at rated load |
AVM
120/280 A |
45 |
120
Kgs. |
3.5
mm |
AVM
120/280 B |
55 |
150
Kgs |
3.5
mm |
AVM
120/280 C |
65 |
180
Kgs |
3.5
mm |
AVM
120/280 D |
75 |
280
Kgs |
3.5
mm |
Type
AVM 275/650

Mount
type |
Shore
hardness |
Rated
load / mount |
Deflection
at rated load |
AVM
275/650 A |
45 |
275
Kgs. |
4.2
mm |
AVM
275/650 B |
55 |
375
Kgs |
4.2
mm |
AVM
275/650 C |
65 |
450
Kgs |
4.2
mm |
AVM
275/650 D |
75 |
650
Kgs |
4.2
mm |
Applications
of Vibro Dampers (Type AVM)
-
Diesel Generating Sets Mounts
- Air
Compressors Mounts (both Reciprocating Type and Screw Compressors)
- Fan
Mounts and Motor Unit Mounts
- Centrifuges
Mounts
- Air
Conditioning Unit Mounts
- Combustion
Engine Mounts
-
Mixer Mounts
-
Crusher Mounts
- Rolling
Mill Mounts
Mounting
Procedure for Vibro Dampers (Type AVM)
1.
Obtain the weight and the Centre of Gravity of the assembly
to be mounted.
2. If this is not readily available, obtain weights and respective
Centres of Gravity of the individual units which make up the
mounted mass. For instance, the engine, radiator, alternator,
flywheel, base frame, etc. from a D. G. set.
3. Determine the position of the Centre of Gravity of the
assembly by reference to two vertical planes at right angles
to each taking moments of the separate units about these datum
planes and dividing the respective sum of these by the total
weight of the assembly.
4. Determine the disturbing frequencies which are usually
primary and/or secondary orders of the slowest speed of the
machine.
5.
Decide on the minimum amount of isolation required. Normally
aim for more than 80%.
6.
With reference to the basic vibration chart, assess the deflection
required on the mounts which when under load will operate
at the desired natural frequency.
7. Decide on the type and number of mounts required after
reference to the static spring rate characteristics which
indicate the load/deflection and load capacity details, bearing
the following points in mind:
a) All mounts must be equally deflected.
b) It is better if all mounts are equally loaded.
8. Fix the mounting positions around the machine so that each
mount will be equally loaded. This is achieved by ensuring
that the algebraic sum of the horizontal centre distances
of the mountings about the Centre of Gravity equals to zero.
This exercise must be carried out in both directions. Long
spans between mounting points should be avoided and normally
limited to 3 to 4 feet although this figure is obviously dependent
upon the structural rigidity of the machine or the sub-base
on which the driver and driver units should be fixed.
9. If it is not possible to distribute the mounts symmetrically
about the Centre of Gravity it will be necessary to take moments
to assess the load reactions at the most convenient mounting
points. This is needed to determine a modified mounting stiffness
requirement to give uniform deflections on all mounts.
Click
here to find the right kind of mount for your machine

|